Análisis PdMA: 6 Zonas de Fallo en la identificación de la salud de tus motores
El personal de mantenimiento eléctrico a estado limitado por años a solucionar problemas con no más de multímetro y megóhmetro. Esto, lamentablemente, no proporciona suficiente información para determinar el tipo de fallo que ocurre en determinado motor eléctrico.
Para reportar con seguridad la condición eléctrica de un motor y asegurarse que la recomendación ha sido tomada en serio, existen 6 zonas de interés conocidas como zonas de fallo que deben revisarse durante la búsqueda de la solución. No tener en cuenta todas estas zonas de fallo podría resultar en la omisión del problema y en la perdida de credibilidad en la habilidad de la solución.
Las 6 Zonas Eléctricas de Fallo
- Calidad de Alimentación.
- Circuito de Potencia.
- Aislamiento.
- Estator.
- Rotor.
- Entrehierro.
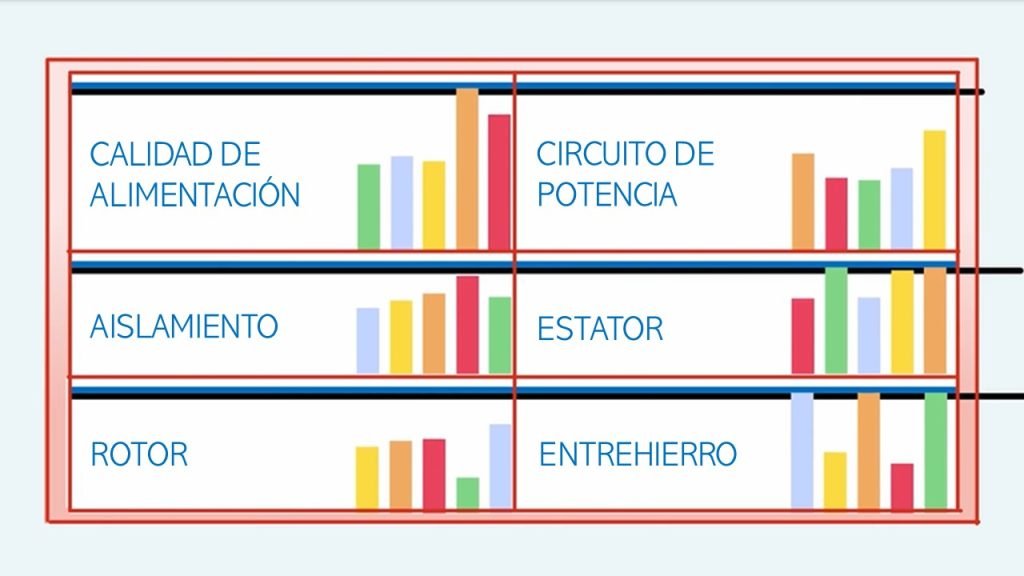
Calidad de Alimentación
Desarrollando un proceso metódico paso a paso, los resultados de las pruebas de análisis de potencia de EMAX rápidamente pueden evaluar 3 de las 6 zonas de fallo. La calidad de Potencia, se refiere a la condición de la señal de voltaje y de corriente. Dentro de los mecanismos que pueden desmejorar la calidad de potencia se encuentran las cargas monofásicas y trifásicas no lineales, variadores de frecuencia, equipos de arranque y de frenado, picos de voltaje, entre otros. Estos pueden causar armónicos excesivos sobre el sistema de distribución el cual puede resultar en sobrecalentamiento del sistema de aislamiento.
La prueba de análisis de potencia de MCEMAX proporciona valiosa información detallada para identificar la calidad de alimentación en el sistema de distribución. Además proporciona también los datos requeridos para la evaluación detallada de un sistema que utiliza variadores de frecuencia (voltaje fase a fase, distorsión armónica, voltaje del bus, distorsión armónica total, diagrama vectorial, dominios del voltaje y corriente, etc.) y sus efectos en el funcionamiento y la condición del motor. La prueba con el MCEMAX le proporciona lo que necesita para saber que hacer en cuanto a decisiones que conducen a un plan acertado para mantener la condición óptima del motor.
Circuito de Potencia
Una conexión de alta resistencia provoca desequilibrios en el voltaje y corriente, los cuales reducen significativamente la potencia de operación. Cuando un motor es alimentado con un circuito defectuoso, se generan con desbalances de potencia como, corrientes de secuencia negativa.
En tanto los problemas se hacen más severos, cae la potencia causando recalentamiento en los componentes adyacentes, daños en el rotor, en el estator, el asilamiento, disminución de la vida del motor, perdida de eficiencia, perdida del motor o explosión. Mientras que los síntomas sean daño del rotor, estator, o aislamiento y la causa esté en el circuito de potencia, el reemplazo del motor por una conexión de alta resistencia solo provocará nuevos fallos en el nuevo motor.
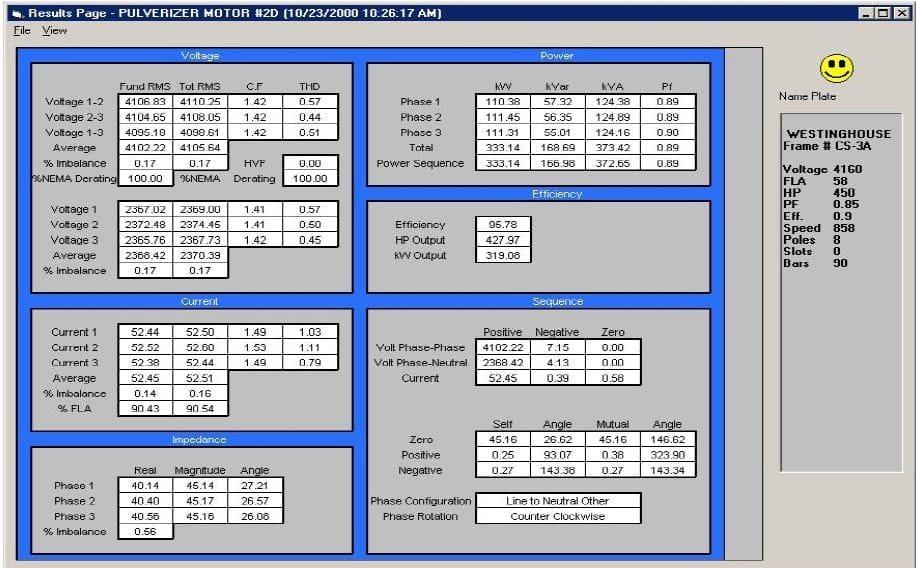
Aislamiento
A pesar de los grandes pasos reconocidos en el diseño de equipos eléctricos, el eslabón débil de la cadena, es aún el sistema de aislamiento. Cuando un equipo eléctrico falla con frecuencia puede ser indicio del asilamiento defectivo.
Muchas influencias externas afectan la vida de los sistemas del aislamiento eléctrico. Estas influencias incluyen la contaminación de la superficie del aislamiento con químicos en el ambiente que atacan y destruyen la estructura molecular, daño físico debido al manejo inapropiado o choque accidental , vibración y excesivo calor por la cercanía al proceso industrial.
Los trasciendes de voltaje en los conductores del aislamiento, así como los picos causados por variadores de frecuencia, pueden disminuir el esfuerzo dieléctrico al punto de falla. El deterioro ocurre en muchas formas y en muchos lugares al mismo tiempo. Por ejemplo, los químicos y/o los cambios de calor, en la estructura molecular hacen que el material aislante se vuelva conductivo, permitiendo que más corriente sea forzada a través de él por el voltaje, provocando una fuga de corriente.
Estator
El análisis del estator usando la tecnología EMAX es realizado, evaluando las relaciones de las fases de voltaje y corriente para cada una de las fases de un motor de inducción AC. Estos valores son usados para determinar la impedancia de cada fase y mostrarlas como un desbalance de impedancia. Las alarmas muestran si el desbalance de impedancia excede el valor base o de referencia.
Cualquier cambio en la componente Real o Reactiva de una fase que es el duplicado de otra fase, indicará un cambio que necesita ser investigado. Otra habilidad en la adquisición de datos sobre la corriente a través del ciclo de arranque de motor. Los defectos de devanado, como las espiras abiertas o en corto, serán identificadas como un cambio en la amplitud de la corriente de arranque.
Rotor
Un método para evaluar la salud del rotor es la prueba de arranque/encendido. Las barras rotas del rotor crean una alta impedancia en el rotor, resultando una impedancia alta reflejada en el estator, produciendo una caída en la corriente y el torque. Otro método es la tendencia de la amplitud de pase de polos en sus bandas laterales. Incrementando la FP, la amplitud de las bandas laterales es indicio de una corriente de línea modulando y que está asociada con el deslizamiento del rotor.
El tercer método para evaluar la salud del motor con el EMAX es el análisis espectral a alta frecuencia, algunas veces referido como el efecto remolino. Las barras rotas o agretiadas crean un cambio de fase en el flujo magnético del entrehierro resultando en múltiples bandas laterales Fp por debajo del quinto armónico.
El 10% de las fallas del motor son causadas por anomalías en el rotor. Esto equivale en el número de motores en un promedio de tamaño de plantas iguales. Recuerde siempre utilizar el espectro general de los métodos de inspección nombrados anteriormente para confirmar y extender la vida del motor, arreglando la raíz del problema y no el síntoma.
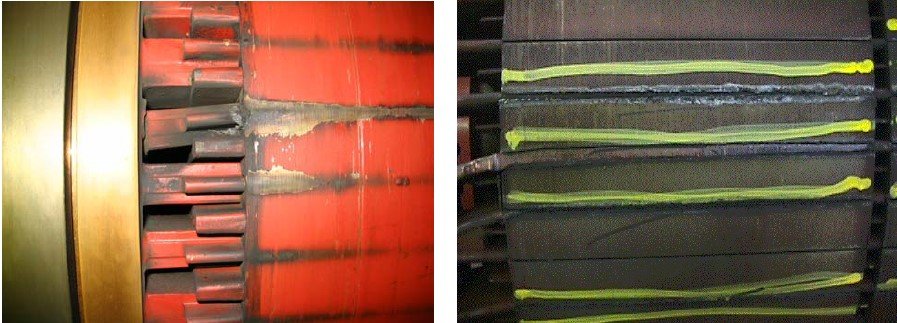
Entrehierro
Excentricidad en el entrehierro desarrollará un desbalance de flujo magnético entre el estator y el rotor durante la operación. Este desbalance llevará al incremento en las vibraciones, desgaste mecánico y posiblemente fricción entre el rotor y estator.
Es importante un equipo que proporcione la información necesaria para tomar las decisiones de mantenimiento acerca de la severidad de la excentricidad. El MCEMAX proporciona fácil evaluación durante el funcionamiento o desenergización del motor. Con la capacidad de la prueba RIC y el análisis espectral de frecuencia, el MCEMAX combina la prueba estática y dinámica para proveer un análisis más comprensivo de esta zona de falla, el entrehierro.
Para mayor información contacta con nuestros especialistas.
Suscríbete a nuestra Newsletter
¡Mantente al día de todas las novedades en mantenimiento predictivo y fiabilidad!